Lean Thinking
The relentless pursuit of the elimination of waste is main concept behind the just-in-time or lean production system. A solid industrial engineering or discipline training is needed to think and implement innovative and effective solutions to eliminate waste.
The amazing fact is that at least 95% of cycle time in a non-lean factory or office is consisted of non-value added activities!
Lean Principle
Perfection is the ultimate goal of lean journey, starting from Customer Value >> The Value Stream >> Flow >> Pull >> Perfection
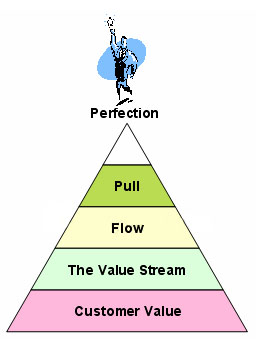
The DNA of Toyota Production System (TPS)
Many companies try to imitate Toyota Production System, but many of them fail to achieve the performance of Toyota. The tools and practices such as Kanban pull system, U-shaped cell, leveled production, standard work, Jidoka, etc. that have received attention are not fundamental to TPS, they are responses to site-specific challenges.
The Rules-In-Use or DNA differentiates TPS from other production systems. In short, there are three rules for Design and Operation, and for two rules for improvement.
Rule 1: Design and perform each activity so that it is structured and self-diagnostic. IE Time and Motion Study; Standard work; Visual Aids; Value Stream Mapping
Rule 2: Design and operate each customer-supplier connection so that it is direct, binary and self-diagnostic. Kanban; Leveled Scheduling
Rule 3: Design and operate the flow-path for every goods, service and information so that it is simple, pre-specified, and self-diagnostic. U-shaped Cell, 5S Visual Aids; Andon Signal
Rule 4: Improve and solve problems regarding activities using scientific method, under the guidance of a teacher (Sensei), as the lowest possible level in the organization. QCC, Kaizen Event; TPM
Rule 5: Improve and solve problems regarding connections and flow-path using the scientific method, under the guidance of a teacher (Sensei), as the lowest possible level in the organization. 5W; Ishikawa Diagram; Jidoka; Taguchi DOE
The key is line workers are doing improvement works under the expert guidance of a Lean Sensei and being fully supported by top management. Besides that, scientific method such as to hypothesis, test and verify the problems/results/improvement plans are an intrinsic part of TPS.
» More Information