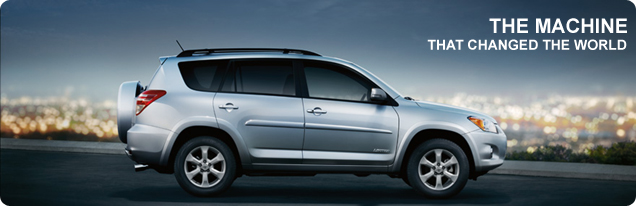
Lean Production is about constantly finding the most convenient solutions possible. It concerns everything from eliminating unnecessary waste to giving customers exactly what they want.
The concept was introduced in Japan by Toyota. That is also where it was refined and tested. Today, decades later, the thoughts and ideas have spread all over the world to thousands of companies.
Lean Production is big. But it gets even bigger every time an individual company and its co-workers implement the ideas and gain success. On the following pages, we will tell you about the foundations of Lean Production and the story of Toyota.
All at once, or a little at a time?
That*s just about as simple as the most basic question in any work for changes ever can be. Because when a company realizes that something needs to be done, it is easy to start questioning almost everything and wanting to move ahead quickly.
It*s fun to make changes and think in new ways. Why stick to the old?
Well - because it is almost never possible to do everything at once. That is not how things work in reality.
By taking many small steps, it is also possible to make corrections along the way. That is the thinking behind the concept ※continuous improvements§ (CI).
In a global world, Lean Production is the solution for a company wanting to work locally.
Companies that prioritize their production optimize their material flows and constantly improve their operations 每 so called Lean Production 每 increase their chances of becoming globally competitive.
Yes, even companies that keep their production in Sweden. With the help of Lean Production, it is possible to achieve more effective production, while developing work on the floor and gaining more capability for innovation.
Many companies have a lot of scope for better efficiency and increased profitability. It*s even possible that Lean Production is a smarter solution than, for example, outsourcing.
A cautious estimate is that companies that have not optimized their manufacturing can make their activities more effective by up to 30 percent! But a condition for this is the ※continuous improvement§ concept, which the next article is about.
This means that well-considered streamlining could lead to more companies being able to prove themselves on the inter¬national market. But this cannot be done overnight; in order to succeed, extensive basic work is required. Our experience tells us that most companies find the process both interesting and exciting.
Reviewing the hard parts of the production, like logistics and automation, is a very important element that is quite simple to carry out. But working with the soft values and creating an organization that really carries out the project and realizes the potential is much more demanding.
Philosophy, approach, culture and long-term thinking
Lean Production is the next step after craft production and mass production. It concerns a philosophy of production, an approach and a culture with a number of principles, a set of tools and long-term thinking.
The governing principles involve eliminating all resource waste, producing more with less, providing the customers with exactly what they want, and creating value and improvement.
This is accomplished through less human effort, fewer ma¬chines and equipment, a focus on using less time and space, and elimination of waste.
The values and norms in the base are built on commitments to customers, owners, employees, and society. The idea is to contribute to the development of society by manufacturing high quality products. This then leads to more job opportunities.
Being a good ※member of the community§ is essential. It is only in the community that a company can become more profitable over time.
There is one company, more than others, that is linked to the principles of Lean Production. Toyota.
Toyota calls this the Toyota Production System (TPS) and this system can be regarded as the origin of Lean Production.
14 principles according to Toyota
1. Base decisions on long-term thinking.
2. Continuous process flows.
3. Control demand.
4. Balance the burden of work.
5. Stop the process when errors occur.
6. Standardization is the basis of continuous improvements and staff participation.
7. Visualization 每 problems cannot be hidden.
8. Use reliable, well-tried techniques.
9. Grow leaders who really understand, live and teach the philosophy.
10. Develop people and groups.
11. Respect partners and suppliers, challenge them and help them improve.
12. Go there; see with your own eyes.
13. Make decisions slowly in mutual understanding; carry them out quickly.
14. Become a learning organization through reflection and continuous improvement.
The true success story for Toyota
In order to illustrate what Lean Production is, a closer study of what Toyota really does is required. Thanks to the historical perspective stretching over 80 years, thoughts and patterns are clearly exposed.
1926 每 Sakichi Toyoda starts a textile factory and invents a mechanism which automatically stops the power-loom if the thread breaks.
1930 每 Kiichiro Toyoda starts Toyota Motor Corporation with his father*s way of thinking and his own ideas about Just In Time.
1946 每 Toyota realizes the great need for productivity improvements. The company decides internally to reach Ford*s level, which then was 2,685 cars every day. It was generally considered impossible for Ford to reach that goal.
In the late 1940s, Eiji Toyota and the production manager, Taiichi Ohno, spent a total of three months at Ford. They studied every detail of the principles of mass production. They observed a number of weaknesses and reached the conclusion that the system would not work well back in Japan.
Therefore, they started experimenting on the home field. They simply tested a number of thoughts and ideas in practice. They started from the idea of a continuous flow and finally replaced it with one-off flow. It is all controlled by Just In Time (JIT) and Kanban, the Toyota philosophy about production control.
Ford, with its large volumes, could work with long set-up times. Toyota, on the other hand, had to reduce the set-up time and, after much hard work, managed to cut this down to three minutes. This meant that it was possible 每 for the workers them¬selves 每 to reset production several times a day.
A fantastic discovery was that it was possible to achieve a lower price per unit with small production runs rather than with large ones. This success was due to decreased warehouse costs for material, quick error discovery and the fact that waste in the form of rejects decreased. The key to success in this work was skilled, interested, motivated personnel.
A depression in the Japanese economy forced Toyota to dismiss 25 percent of their employees, but a compromise gave the remaining personnel lifetime employment and pay linked to seniority.
The workers were clearly expected to contribute to the company development. This also created a corps of willing employees who did not need to worry about being fired.
Now they started performing new experiments with teams that worked together and were responsible for cleaning their workspaces, repairing certain tools, and performing quality controls. Add to this a collective and constantly ongoing improvement work with the support of engineers.
Ohno noted all the waste of material, time and human re¬sources. He also saw that all the specialists were not bringing much value to the customers. The workers could do this job better 每 and they had the lowest status at Ford!
Ohno also established that errors in assembly were multiplying quickly and required a lot of correcting. A stop string was therefore installed above every workstation. When a worker could not solve a problem himself, all he had to do was pull the string. As a result, the team gathered at that workstation to find the cause of the problem. At first this led to constant stops but, as time passed, they became less frequent and, at the same time, quality improved.
The flow was organized with small buffer stock, which made the production system sensitive to interruptions. According to the traditional approach of mass production, this was impossible. But, according to Ohno, it was extremely important.
When all the flaws were visible they could be dealt with easily. An increasing number of processes were correct from the begin¬ning. Fundamentally, innovative skills were what were needed.
It was in the 1970s that Toyota Production System (TPS) was born. Outside Japan it was a completely unknown concept.
TPS is a completely different way of developing and manufacturing products, a revolution involving the entire company from top to bottom. The starting point was customer needs, which affect every element of the company. While traditional mass production was focusing on costs, Toyota was concentrating on speed and short lead-times which gave lower costs and higher quality.
Lean Production now and in the future
The example of Toyota is extremely pertinent today. Toyota has now overtaken General Motors as the world*s biggest car manufacturer. Just a few years ago, this was considered impossible.
Naturally there are many factors which have been vital for Toyota*s success. But Lean Production is, without doubt, the most important. Even if every company has its own unique conditions, they can all learn something from what Toyota has achieved and is still doing so incredibly well!
Obstacles 每 common circumstances
The latest fashion. The company is constantly switching between different options and often without any plan. This is often based on what the last consultant said or what the boss heard at the last seminar. It is often due to a lack of competence.
Islands of success. The company starts initiatives within limited areas and these do not spread through the company. Often this is because insufficient resources are dedicated to improvements.
Too much at once. More initiatives than can be handled efficiently are started. Reasons for this can be the inability to finish or the lack of ability to direct projects for change. It can also depend on external demands that are being point¬ed to by a customer or supplier.
Comprehensive ways of avoiding obstacles
• Production improvements are seen as a process, not a project.
• Leadership must support the improvement work.
• Management must realize that Lean Production is another way of producing, not just a set of methods and tools.
• The implementation of occasional initiatives is not enough.
Many small steps are the road to success
During the &80s, industry focused on target-con¬trolled groups and on delegating responsibility and authority in order to create an effective, attractive work organization.
Work development became a central concept. One of the problems with committing to work development was that it required extensive training and substantial changes in organization and wage systems. During the &90s, focus shifted from work development to quality thinking in every part of the organization - Total Quality Management (TQM). An important part of TQM is to involve all the employees through continuous improvements. Continuous improvements can be defined as continuously and systematically improving the activity in a series of small steps.
During the period 1993 to 1998, a study was conducted of companies that succeeded in implementing TQM and work development on the workshop floor. The study showed that there were several obstacles blocking the way of the implementation work. Management attitude, ability and previous experience are all of crucial importance for the way in which the company works with TQM. Three different strategies for quality work were identified: control strategy, motivation strategy and work development strategy.
Three different strategies
The control strategy means that the organization is hierarchical. The operators have limited authority and responsibilities. The quality is controlled by parties other than the manufacturer of the products. The quality systems that exist are bureaucratically built and not precision oriented.
The motivation strategy means that the staff is motivated to produce better quality by increased understanding of the custom¬er*s demands. The staff, including the operators, is trained in different quality tools and takes part in improvement activities. No structural changes are made in the work organization or work division.
Work development strategy means that changes are made in the work organization and work divided in order to create conditions for better material and information flows. Target-con¬trolled groups are created, and work development is viewed as an important ingredient for creating interest in development of the activity. Continuous improvements are used to refine and develop procedures and work methods.
The work development strategy is the strategy that best cor¬responds with the basic principles of Total Quality Management. This is, to a great extent, a result of the focus on processes. The strategy is also of interest since it combines the earlier concentration on work development and the concentration on proactive, quality development with the focus on continuous improvement that is becoming increasingly common today.
Change in incremental steps
The challenge is to combine continuous improvement with work development. By starting work for change in small steps, there is a possibility of creating good working conditions and an effective activity without taking too big a step. The idea originated in our experience as consultants when we found that it is easier for companies to accept continuous improvement than to accept drastic change in an initial phase of the change work.
Continuous improvement where the employees participate with knowledge and ideas are easier to understand and to visualize than a complex, new way of working with an altered power structure. Continuous improvements simply pose less of a risk than work development.
How to start?
Establish has worked with a number of companies that have be¬gun a methodology of working for continuous improvement and work development. The method of working is based on a technique called 5S (Sorting, Systemizing, Straighten up, Standardize, and Secure) and on creating teams which are formed around a geographically-defined area.
5S derives from Japanese and stands for: seiri, seiton, seiso, seiketsu and shitsuke
• Sorting 每 Sort out roughly and eliminate what is not needed for the job 每 all that is broken and in the way.
• Systemize 每 Mark and place information and tools that are often needed for easy access.
• Straighten up 每 This involves not only cleaning in order to make a better impression, but it also means identifying leakage and solutions which facilitate the cleaning and, preferably, eliminating the need for straightening up.
• Standardize 每 Establish procedures so that every one knows what is expected, where things are, and how tasks should be carried out.
• Secure 每 Nothing is constant without continuity and procedures, and the methods of working must be restrained so that work remains efficient. Securing also means creating a safe working area and work¬place, thus securing the working environment.
By having a team focus on a defined area and the team members shaping their workplace, a foundation is built for an ongoing development of their activity, in small steps and by a continuous, systematic process. Once the team or the company feels it is ready for the next step in the improvement work, a company-adjusted certification can be used to decide its status with regard to the 5S and how well the group members work together.
5S does not involve major structural changes. It is easy to understand and can be used directly in the daily work. It provides rapid results and is applicable for the entire company, and can therefore, be used to involve the entire staff. This is shown here through a comparison of some of the most common directions of improvement work today. See Figure 1 below.
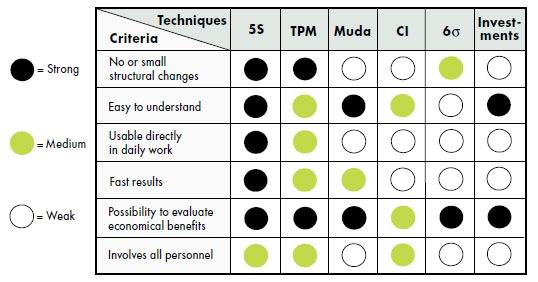
Fig 1. The figure shows how well the different focuses
fulfill the characteristics viewed as urgent in the start-up.
• TPM stands for Total Productive Maintenance and involves a focus on the total efficiency of the equipment and extensive operator maintenance.
• Muda stands for waste and is a focus on eliminating transport, waiting, overwork, warehouses, and quality flaws.
• CI is continuous improvement without any certain focus; for example, a program of suggestions.
• 6 sigma (6考) is a project-based way of working with a focus on variety and economic results.
• Investing is the traditional way of developing activities where production techniques or process developers develop production and productivity.
It is important to find a way of making the start up as simple as possible so that the company realizes the possibilities immediately, and does not face too much resistance in the beginning. Compared to other techniques, 5S is a good way of starting up improvement work.
How to think?
Our adaptation of the 5S way of working involves elements which are normally not linked with 5S. These are the possibilities of evaluating economic advantages and seeing how the staff feels about the start up of continuous improvement and work development.
It is important to measure the economic effects of the continuous improvements, but also to find out what the staff thinks of the new way of working. The goal is to build a foundation for the future development of the company over a long period of time. Hence, we have to see economic profits as well as a high level of motivation based on real understanding.
In order to succeed in starting up and implementing continuous improvement and work development on a basic level, there is a structure of five phases:
The first phase is Project consolidation, which means that the conditions within the company are investigated.
The second phase is Management training and involves management being taught about continuous improvement, the connection to work development, and how teams can be built with continuous improvements as the way of working.
The third phase, Enablement, identifies enthusiasts in the organization and coaches them to be a link between different groups and work as a method support for continuous improvements and the forming of groups.
The fourth phase, Team training, means that each group is coached and trained to be better able to develop its own work¬place and gain understanding about the purposes.
The fifth and last phase, Support, means that management, the enablers and perhaps external consultants help the organization to follow up the results of the work with continuous improvement and work development using different evaluation tools.
New energy constantly needed When the work on continuous improvement (CI)and work development (WD) has been launched, many companies are satisfied and begin focusing on something else. There is a danger in this since continuous improvements and work development always require new energy and have to ad just to the company and its surroundings in order to survive. One way of achieving this is to align the improvement work to the company*s central goals. Recently presented research based on the improvement work and work development within Swedish manufacturing industry shows that the work for continuous improvement must be connected to company goals in order to result in the expected payoff. We want to initiate powerful improvement work that not only works over a long period of time, but also carries on developing as the staff becomes keener about contributing to the company*s development. This can be illustrated with steps: one for continuous improvements and one for work development, see Figure 2 below.
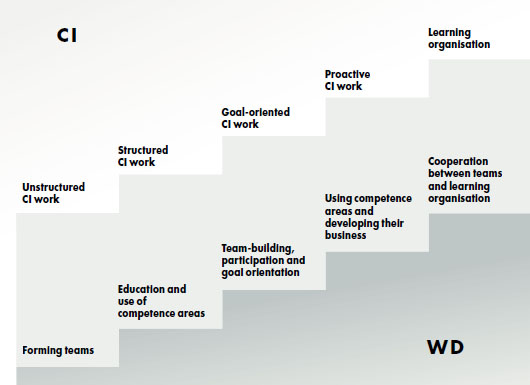
Fig 2. The figure shows where the model is active.
The upper ladder shows stepwise development of the CI work at a company.
The lower ladder shows stepwise team development at a company.
What are the most important factors for success? Success, not only in starting up but, above all, in implementing powerful work on continuous improvement (CI) and work development (WD) according to Figure 2, involves a number of important aspects. Figure 3 below gives a picture of these vital elements.
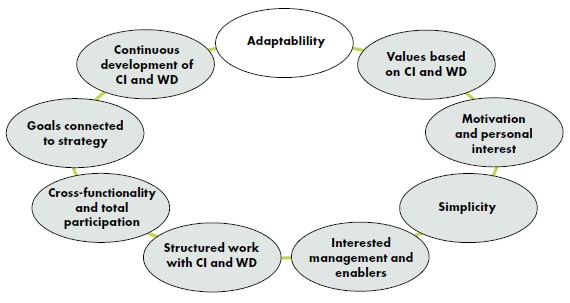
Fig 3. Implementing powerful work on continuous improvements (CI)
and work development (WD) involves a number of important aspects.
Adaptability is the way of working which is created for continuous improvement. Work development should be well adapted to the particular company, but also adaptable to future changes in the company and its outside world. Values based on continuous improvement and work development refer to a fundamental value in the approach of continuous improvement and means that small improvements in a systematic direction are seen as an important ingredient in the development of a company. In the same way, a fundamental value in work development is belief in the team as a vital ingredient in the creation of interesting, efficient companies. These values have to be established in the organization in order to give credibility to the new way of working. Motivation and personal interest state the importance of reaching the areas the staff find important through the new way of working. It also needs to attract the personal interest of key participants.
Simplicity is central since one basic element of continuous improvement is simplicity. This should be embraced and not complicated by administrative systems weighed down by processing suggestions, the wage system, material management systems, etc.
Interested management and enablers refer to the importance of the people in charge not just saying that they support an approach, but demonstrating this in practice as well! In spite of this, there is a need for personnel with certain skills and personality who are good at supporting their colleagues and working with continuous improvement. You might claim that without enablers, management would become burnt out, and vice versa.
Structured work with continuous improvement and work development underlines the importance of structured implemen¬tation in order to establish the new way of working. It allows it to survive, but also makes clear the importance of a structure for the way of working itself so that everybody knows, how groups should meet, suggestions be processed, and goals followed.
Cross-functionality and total participation is the realization of the possibility, through continuous improvement, of using all the hidden potential in a company. That is why it is particularly important for every one to participate. This is also vital when it involves work development. As the groups develop, their abili¬ties to solve problems increase and, as their responsibilities in¬crease with more assignments being passed their way, it is only natural that improved cooperation between different groups and functions is a result.
Goals connected to strategy refers to the fact that working with continuous improvement and work development should be con¬nected to the company*s long-term strategy to gain legitimacy in the entire organization and to receive the proper focus. An important part of linking together the new work method to the company strategy is to use clear goals for what the individual group should achieve.
Continuous development of continuous improvement and work development means, for example, that as the goals of the 5S-work are reached, it is important to develop the new way of working. This means that the staff needs continuous training and more knowl¬edge to be capable of operating increasingly complex improve¬ments together with other functions. The increase in skills is also a link in establishing continuous improvement and work develop¬ment as vital ingredients in the company values and their strategy.
Active management in a good structure
The presented factors can be summed up in the importance of the company management being actively involved, and of the existence of a well-defined structure for establishing continu¬ous improvement and work development.
This work should be able to be clearly connected to a compre¬hensive development strategy. Management can not handle this itself, but needs support from enablers who have time to support the organization and the improvement work and to form a link between different personnel categories and functions. Enablers create, together with the rest of the organization, forceful work with continuous improvement and work development, with goal orientation, simplicity, adaptability, and cross-functional think¬ing being key words.
It is important to examine the conditions of one*s own orga¬nization before starting up a project with continuous improve¬ment and work development. There are a number of important factors to address, but it is difficult to know in advance what the solutions will be for a particular company. Some companies embrace a new way of working right away since they have no preconceived ideas, while others are more careful for fear of doing something wrong.
How do we identify obstacles?
It is important to identify the factors that determine success or failure in the implementation of a new way of working.
The obstacles can lie within different areas and might in¬clude previous experience, management*s capability with re¬gard to work for change, insight regarding the need for change, the type of activity, and the cooperation between the unions and the company. When starting up a project for change, it is important to consider what can delay a change process. This could be individual people, poor procedures or the inability to get things done. In such cases, it is critical to deal with these obstacles, otherwise an eternal struggle will exist between the old and the new. Figure 4 illustrates the need to minimize the opposing powers that restrain change and increase the driving forces that work for change.
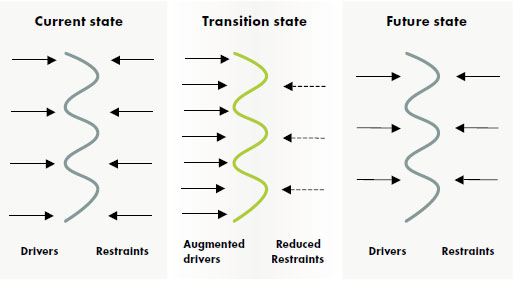
Fig 4. The figure shows how more power and resources are introduced
in the transition state to be able to make a change take place.
Good enablers offer a clear supply of focus and power, which is excellent when working for change. It is best to not lose these enablers as soon as the work is done and the changes are made, but only reduce the number. To identify the obstacles more easily, you can regard a change as a flow that can be stopped or weakened by obstacles in the organization and its surroundings. See Figure 5 below.
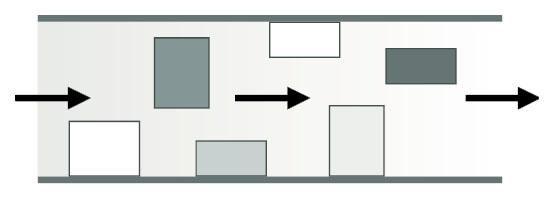
Fig 5. The rectangles illustrate the significant obstacles that are encountered
when trying to implement a new idea and finally make it sustainable.
One way of identifying these obstacles is to thoroughly perform the project consolidation mentioned previously in the article. Here, there are two important things to keep in mind. The first thing is to interview people from every part of the organization and on all levels, and to ask them to identify obstacles and pos¬sibilities. The second thing is to review how work with changes has been carried out previously within the company.
How can we go forward?
From the factors presented in Figure 3 and the above discussion about obstacles, we can point to a number of important pillars in the building of sustainable development of the continuous improvement and work development.
The most important thing is the active, clear involvement of management in the process.
Management also gains trust by having a clear plan or pro¬gram for how it plans to develop the company. That plan or program should contain a structure of values in which con¬fidence in small, continuous improvements and a continuous development of the content of the work and the work organi¬zation are central.
Since a company*s management and the other change sup¬porters might lack both time and expertise, it is important that there are forces in the organization that facilitate and support the changes locally on the different work places - enablers. These forces, programs, management, enablers, and values should work together. This is easiest to accomplish by having a clear structure on how the way of working should be implemented and expected results.
When the way of working has been decided, the base just mentioned should be used to gradually develop continuous im¬provements as well as work development. Important key words in the continuous development, after the work with 5S has start¬ed and the groups have been formed and started to develop, are goal orientation, simplicity, adaptability, and cross-functional thinking 每 all to avoid suboptimization. This can be illustrated as per Figure 6.
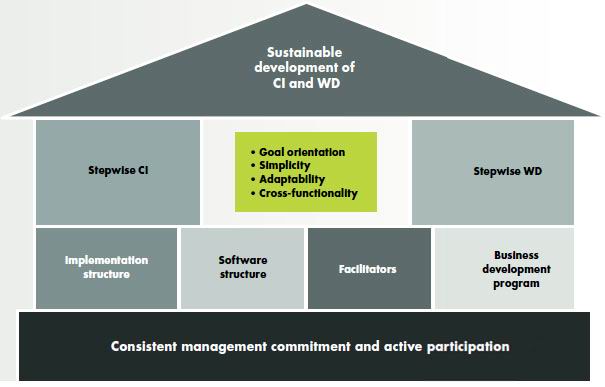
Fig 6. The figure shows how the different parts
of the model support WD-based CI work.
The above approach provides excellent opportunities for seeing a strong development of the work with continuous im¬provement and work development and, thus, opportunities for increased competitive strength for the industry. A company that succeeded well in their change work, and managed to keep it alive, is Scania. That is where we got the idea of the house anal¬ogy to represent the work for changes in a company.
» More Information