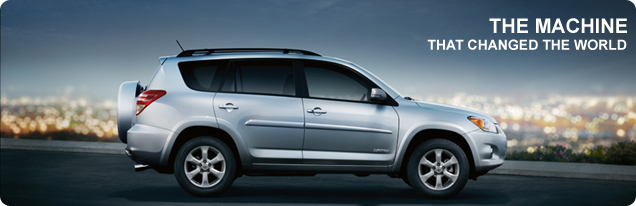
Introduction
An in-depth interview with Professor Monden about his renown work, Toyota Production System, and his ideas about Toyota and the spirit of kaizen in today's manufacturing world.
Profile
Yasuhiro Monden
Ph.D., Professor
Faculty of Business Administration
Mejiro University
(Professor Emeritus, Tsukuba University)
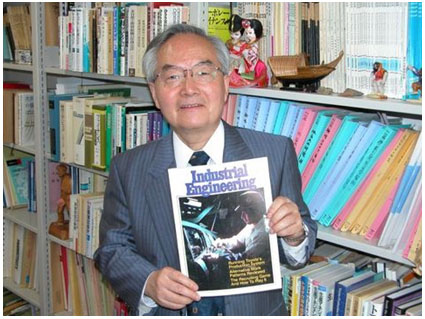
Fig 1. Professor Yasuhiro Monden Ph.D. in his Mejiro University faculty office,
holds up a copy of the original issue of Industrial Engineering that published
his first English paper about the Toyota Production System.
Q. Why did you decide to write the world famous book "Toyota Production System"?
A. Initially I had been a professor of accounting instead of a professor of production management or operations management. In the field of accounting I majored in managerial accounting and then as one of the topics of managerial accounting there was the topic of cost reduction. Someone told me that the Toyota Production System (TPS) or KANBAN system was a very useful way for reducing costs so that's why I visited Toyota and its suppliers to find out about the TPS. I decided to write the book in 1979 but originally, I wrote an English paper entitled "What makes the Toyota Production System Really Kick." That was the first paper systematically written about the TPS. The title was decided on by the editor. Before I sent the manuscript to the publisher of the Industrial Engineering I sent the manuscript to Toyota to get permission to publish it in this United States journal. They have translated my English paper into Japanese to check the content. I still have their Japanese written translation. They gave me permission. Later they said that Mr. Ono checked the contents and by coincidence, it just happens that the other day I was clearing the bookshelves in my office and I found a letter from Mr. Ono. Anyway, when this issue was published in January 1981 there was a very big response throughout the United States. At that time, I was 40 and I was a visiting associate professor of The State University of New York at Buffalo where I was teaching several accounting courses. I received a lot of phone calls at my office in buffalo and I was invited to give many talks at various places about the TPS, in total 10 times in half a year.
Q. Have you ever met Mr. Taiichi Ohno?
A. Yes, I did meet Mr. Ohno. He was said to be a very rigorous person to the managers of the plants but he was very generous and kind to me so I was very happy. He wrote the preface to my TPS book and also published another book on the TPS with me.
Q. When you wrote your book what condition was Toyota in?
A. At that time, there was severe trade friction between the United States and Japan. That was the automobile trade friction and the situation was very similar to the current situation in that the oil price increased and their big cars couldn't be sold but Japanese small cars had good fuel consumption and they sold very well. As a result of this there was a very severe conflict between the two governments and the Japanese automobile makers made the decision to make voluntary restrictions to refrain from exporting their cars to the United States. Of course, they don't have the same situation now. At that time they exported most of their cars but now they have installed their own plants in the United States and their major suppliers have also installed their plants in the United States as well. That's then considered as local content when they use their group plants in the United States.
Q. What was the hardest part of writing the book?
A. Currently, there are numerous books on the TPS but most of them are just describing the kaizen part of the system but the unique point of my book is about the computer-based information systems. In the way for instance that the production information system is used in the MRP (materials requirement planning). In addition, I have written about the technical parts of the system such as the mixed model assembly scheduling techniques (mixed model assembly line), which is called the Goal chasing method. This kind of technical part of the system is very important but no other book has gone into detail about it.
Q. Your book is a very academic and scientific analysis of the TPS. What kind of research did you have to do?
A. Some level of mathematics. This is the field of operations research or industrial engineering and maybe to develop those kinds of techniques you need to study at an engineering school rather than social science or liberal arts departments. In my case I was in the middle of the two.
Q. Did you have any special help from Toyota in writing these algorithms?
A. That was the most difficult part. Some of the technicians and experts at Toyota also belong to various academic associations and sometimes they make presentations there, such as at the academic association of industrial engineering. I'm also a member of this kind of association and when I checked the program and I could see that someone from Toyota was going to give a talk I would attend the lecture and get the information I needed. They not only displayed the manuscripts etc. but they would even write the mathematical models themselves and as the proceedings of the association these would be broadly published.
Q. What is your personal definition of the TPS?
A. I think the most important feature of the TPS is the "Just-In-Time" (JIT) concept. This is the concept of a system to make a product that is needed at the right time, in the right quantity. Many books just emphasize kaizen but JIT is the central part of the TPS.
Q. Which parts of the Toyota Production System do you have the greatest interest in?
A. As an academician I have written many papers on mixed model assembly scheduling models. I have also developed original models and simulation studies that are called heuristics models. That is the part that interests me from an academic view point. However, from a pragmatic point of view, when I visit any plant I always like to see how the single piece flow production is actually being made, even though the units may not be single but small lot production. If this is not being realized then I always suggest how to approach the single piece or small lot production.
Q. For those readers who buy your book, which sections would you recommend they read most carefully and what should they pay attention to when reading those sections?
A. For the beginners, I obviously recommend that they read chapter number 1 intensively. Whilst for those people who have already studied the TPS to some level I would suggest that they read the chapter on how to introduce the system in to their plants. Even although there are various techniques and advanced techniques etc. to be learned there also exists another topic, which is how to actually introduce the system into the plant. There are various steps required to introduce a TPS into a plant and that is another problem, which is not a part of the TPS itself. However, for those responsible for introducing the system it is also a very important topic.
Q. How has the Toyota Production System evolved over the years?
A. When I first visited Toyota and also initially Daihatsu motor company, that's a mini-car maker that belonged to Toyota but now they are a subsidiary company with Toyota owning more than 50% of their stock, I thought that this was a very severe way of manufacturing. Especially for their workers who had to work very hard, although they say this is efficient but not so hard. They said that they were trying to abolish the wasteful actions of workers, exchanging wasteful action with other value-added action but to me this was very hard work. However, since 1992 when Toyota established a new plant in Kyushu, the Fukuoka Miyata Plant, things have changed. Ergonomics, the field of human engineering, was introduced in to the operations management of Toyota's plants so that even women or elderly people could easily work in the plants without becoming fatigued. The main reason for why Toyota changed their production system to incorporate ergonomics was because of the difficulty of getting employees. That's one of reasons why they have established their plants in Kyushu, so as to be able to get more employees. Although most of their plants are located in the Chubu area near Nagoya, they have had to move to Kyushu to get workers. And with the decrease in younger people they have had to employ more women and elderly people.
Q. Since the TPS was first established is there anything that still continues the same at Toyota?
A. Yes, that's the spirit of Kaizen for continuous improvement.
Q. What are the biggest differences between introducing the TPS into a Japanese plant and an overseas plant?
A. In Europe and the United States, there is a special industrial relations, craft union. Each worker who works in a certain division must belong to that country's craft union. For example, a turner belongs to the turners' craft union, that covers the whole country, and a welder joins the welders' craft union. They are guarding their own working area, but the TPS assumes multi-skill workers so the multi-skill worker can not be cultivated under the craft union system.
Q. Is it possible to implement the TPS without multi-skill workers?
A. It's not easy but a partial implementation is possible. Even though the multi-skill worker is not used you can still introduce the system partially, for instance, the setup time reduction system and those kind of techniques could be introduced anywhere.
Q. Are there any other major differences between Japanese and overseas manufacturers?
A. There is big difference in the suppliers system and the relationship between the maternal company, in other words the final car maker, and the vendors. Until the end of the 1980s most of the suppliers were just the parts manufacturing divisions of the final assembly maker. This was the case for General Motors, Ford, and Chrysler etc. However, in Japan the suppliers have manufactured most of the parts outside of the assembly makers, and the KANBAN system, or parts requirement system, is entirely different. In Japan they have a very long term contract for using parts but it is said that the contracts between assemblers and parts makers in the United States used to be very short, just one year. However, after the 1990s many companies changed their system. General Motors established a big parts maker called Delphi, and they separated their parts division into another independent company and a long time contract relationship was introduced,
Q. What is the advantage of having a long contract?
A. You can have a more reliable relationship when you have a long term contract because, for example, the parent company can send their staff to teach how to make improvements. Toyota is always doing so and the KANBAN application is also very easy to implement. In addition, the assembler and parts maker can jointly develop custom parts. These kinds of things are difficult to achieve over a short period of time.
Q. What are the biggest differences between theory and practice when considering the implementation of the TPS?
A. I first taught about the TPS when I visited Singapore at the invitation of JICA (the Japan International Corporation Agency), a kind of governmental agency, to teach various companies. I also visited Thailand, USA, Taiwan, Argentina, Sweden, China and Austria. As a consultant I always examined if the production was going smoothly, that's the point I mentioned before, whether or not single piece or small lot production is being made or not. This is hardly achieved in practice. Also, when I look at the various processes I check to see if the balance of the workers' tasks is being achieved or not. If some people are very busy and other people are not so busy then that is not a good situation.
Q. Is it difficult to balance the workload?
A. If the production is being made with a big lot size then it is not easy to find a good balance. The bigger the lot size the harder it is to balance because inventories will be built up between the processes and these will hide the unbalance problem.
Q. The TPS has had a very big influence around the world but what influence has Toyota had on the Japanese manufacturing industry itself?
A. It has had a very big influence during the past 40 years, which is when the benefits of the TPS first became apparent. People discovered the TPS when the first oil shock hit Japan around 1972-1973, because they had to reduce costs. Everyone heard that the TPS was really useful to reduce costs and from that time the TPS became very popular around the country.
Q. What percentage of companies in Japan uses the TPS?
A. I think that most manufacturing companies know about what TPS is, theoretically at least, and have introduced the system partially. Even the chemical industry or those companies with large scale equipment are using the TPS as well.
Q. Is there any room still left for improvement in the TPS after all these years?
A. I believe so but I don't know what kind of direction they will go.
Q. What is the biggest challenge faced by the TPS for manufacturing in the future?
A. The shortage of human man-power is the biggest problem in Japanese plant management. One of the ways to resolve that problem is, as I said before, is to humanize the production system and employ women and elderly people. Another way must be the utilization of automated machines so that even though a company couldn't employee so many workers they can still respond to the growing demand of their product. But that is part of the field that the traditional TPS has not been challenging. It is the field of mechanical engineering rather than plant manufacturing, operations management or industrial engineering. This is one of the biggest challenges that manufacturing companies will face in the future
Q. What is your current project?
A. My current research topic is inter-firm relationship or network organization. That includes product manufacture, parts manufacturers and sales dealers of automobiles. That topic includes production management, organizational economics and managerial accounting. All three topics are my major fields that I have studied.
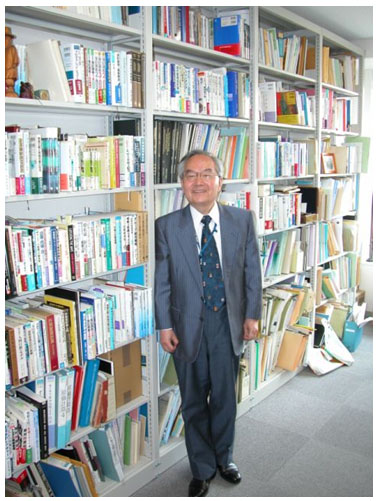
Fig 2. Professor Monden, in his Mejiro University faculty office
Interview by Lean Manufacturing Japan editor: Warren Harrod
» More Information