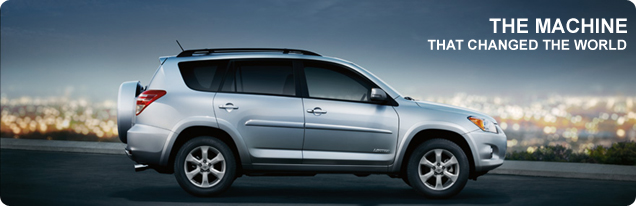
Edited by Warren Harrod
Profile
Tomoichi Sato
Senior Deputy Manager, PMP (Project Management Professional)
EPC Technology Advancement Group, No. 2 Project Division
JGC Corporation
Tomoichi Sato has been serving in system analysis and project management roles for both domestic and overseas projects. He has been involved in both the design and implementation of systems for production planning, advanced scheduling, ERP, MES and e-Procurement. He is a Registered Management Consultant for Small and Medium Enterprise (PMP). Tomoichi Sato has also authored a number of books including "Introduction to Advanced Production Scheduling", "The Art of Time Management", and "Understanding BOM/Bill of Materials" (in Japanese).
1981 MA. Graduate School of Tokyo University (Chemical Engineering).
1985-1986 Visiting Researcher at US East-West Center.
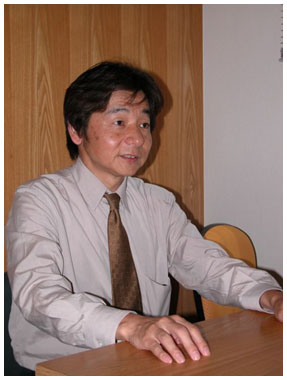
Fig 1. Tomoichi Sato, at the Lean Manufacturing Japan editorial office,
talks about his experiences in the manufacturing industry.
Introduction
An interview with Tomoichi Sato about the importance of planning in the manufacturing industry and how the different levels of planning interact.
Q. Production scheduling is only one part of the overall planning and management of production. There are many words that we use such as Production system, Production management and Production planning etc. Could you first introduce each of these topics and explain how they work together?
A. First of all, I would like to start with the definition of the production system? The production system is a system to convert demand information into products. This system is composed of humans, machinery and the space provided by normally a kind of building. They are generally called resources, human resource and mechanical resource. Sometimes we also include utility because this is also a type of resource. Using these resources, the production system converts demand information into the products to be supplied.
The conventional view is to regard raw materials or parts as input into the production system which converts them into the products (Figure 2).
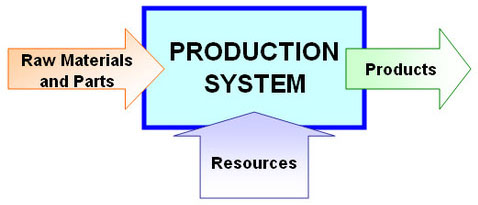
Fig 2. The conventional view of the Production System
However, my interpretation is a little bit different. The main input is not the raw materials or the parts but the demand information. My perspective is that production system converts demand information into products with supporting resources and raw materials and parts. This is what drives the overall system. From the conventional point of view, you can produce products without any demand information. However, as a consequence, you may have a lot of products in your warehouse that nobody needs. This can still be called production, but you are producing products with no value. The production system, which produces added value, is driven by demand information (Figure 3).
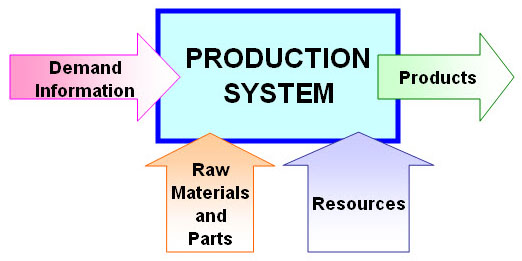
Fig 3. Tomoichi Sato's interpretation of the Production System
Of course, there is a process to transform this demand information into a product specification, manufacturing process information and work instructions or a production plan and production schedule. These activities are called engineering. Engineering transforms demand information into a kind of blueprint of the product. In addition, the production control function creates the production plan information. Inside of the production system, based on these two pieces of information, people produce products from the parts and raw materials by using resources. This is the production system.
Q. So within the overall production system, you have product management and production planning.
A. I'd say that the terminology here is a little bit confusing, or used differently. The activity to create a production plan is what I would call production control. Control is a kind of more detailed activity compared to management.
Q. Is this what we call SEISAN KANRI (production control) in Japanese?
A. One of the very confusing things in Japanese is that we only have the one term, KANRI. However, in English, we have management, control, and administration. These are different things, right? Normally management is a higher activity to oversees things, to organize people and resources, and make the system work properly. Control is more precise. Management creates the system, whilst control just operates the system. So, control is usually focused on the near future and monitors resources or people. This is a kind of feedback control, in a sense. To the contrary, management words as "feed forward". Administration is a kind of supporting work. We should be very careful when we talk about KANRI. So, I try to avoid using the word KANRI. Instead, even in Japanese, I try to use the words "manajimento" or "control".
Q. So what is the role of the production management within the whole production system? The view is that the management is at the top giving the orders, but in fact, is their role to support the production?
A. Let's just imagine there is a kind of craftsmanship. My father-in-law was once a craftsman. Later he became a manager within a small company, but as a starting point, he was a craftsman of wooden barrels, the smaller ones used for daily washing and the larger ones used as a bathtub etc. In the good old days, the craftsman himself received the order from the customer. Then he would pick the raw material, in this case wood, cut and assemble it. Everything is done by his own hand. And finally he delivers this product to the customer. In such a world, all of these things are done only by the craftsmen. No other activity is required. Of course, there will be some selling, invoicing and collecting things but these are done by a salesperson. In my father-in-law's case, that was done by my mother-in-law. When his business began to grow he then hired more craftsmen. As the production volume increased, what happened? There should be someone who is specialized in the purchase of raw materials and wood material, because handcrafts heavily depend on the quality of the wooden material. And also, there should be a specialized guy to store the raw materials and the finished products, take things from the warehouse and deliver products to the store. Although there are now many different kinds of specialized jobs, the core work which creates added value is still focused on the cutting and assembling. This is what we call direct work which creates added value (Figure 4).
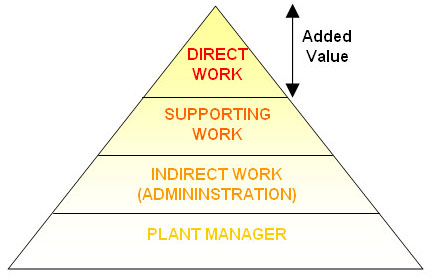
Fig 4. Only the direct work creates added value
And the other work, for example, the purchasing, warehouse keeping and transportation work, these are supporting work. As the volume of work increases, the specialization of this supporting work increases the productivity of the craftsman. If there are no other people to assist then the craftsman himself has to go to the raw material supplier and negotiate, or he has to take things from the warehouse etc. In this case, his time to focus on the direct work is limited. That's why to increase the productivity of the craftsman's direct work; this kind of indirect work is shifted to the supporting people. And the more the business volume increases, then the more specialist jobs will be required, for example, someone who is specialized to deliver the raw material to each craftsman or someone who has to set up the ordering or even someone who prepares the tools needed everyday. Only the direct work creates added value. We also have the supporting work as well. However, taking raw materials from the warehouse to the shop floor doesn't create added value. So the work is necessary, but it isn't added value work. The work that is necessary, but isn't added value work, we call supporting work. We also need some specialist work as well, which is indirect work. For example, scheduling, purchasing, selling or accounting, which we can call administrative work. These people do not contribute directly to create added value, so why are these people required? These people only contribute to increase the productivity of the direct workers. In the production system, the most important people are the laborers working on direct work. The other people are helping these people so that they can work effectively and efficiently. In the larger sense, we call this kind of thing, production management (Figure 5).
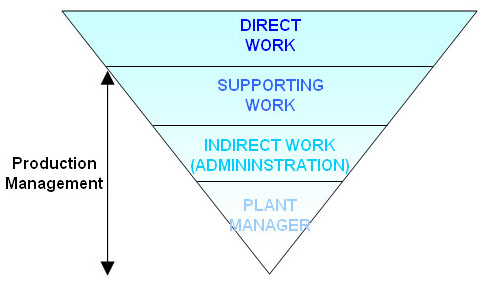
Fig 5. Production management is there to support the direct work
Q. What is the biggest problem for management when you try to manage all the different parts of the company, to make sure that it all does work together correctly?
A. I'd like to point out two different things regarding your question. One thing is how do we measure the effectiveness and efficiency of this production system? The purpose of management is to make this system effective and efficient, right? Another thing is that because the core part of the production system is human, how do you make people work comfortably and happily? This is the human factor. Both of them are very important. Let me explain about efficiency and effectiveness first. In Figure 6, we have one axis as the time, and the other axis representing product quantity. We also have a cumulative curve, which represents the demand from the customers. Sometimes a steep rise may mean higher demand, and in another season there will be lower demand. There is another line for the production supply of the products. If the supply curve is above the demand curve, then what exactly does it mean? All the time that we have more supply than demand it means that we are doing things ahead from the viewpoint of time. Or, if you look at the quantity then it means that we have more stock available. How about when the supply is less than demand? If we have a shortage of supply then that means the time taken to deliver the product is being delayed. So, it's obvious that the lower supply curve is quite ineffective. Are we effective from the upper supply curve?
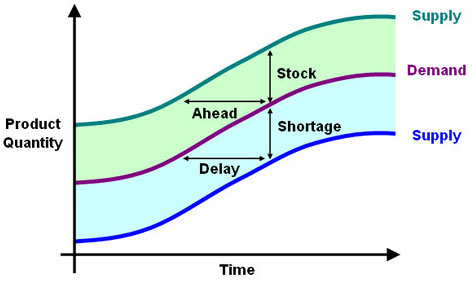
Fig 6. The relationship between supply and demand
Q. I guess you can say that as far as your customer is concerned, having too much stock is better than having a shortage of stock, but this is going to cost you money.
A. That's right, so the best situation is to make the supply line perfectly fit the demand line. In an ideal world this would be fine but in the real world anything can happen and it does. So, normally, the supply curve is like Figure 7. Sometimes there is a shortage and sometimes there is too much stock. Thus, the goal of the production system is to match the supply curve as closely as possible to the demand curve. This is effectiveness. We can measure effectiveness in two ways, through the time line and on the quantity base. In the time line, we are referring to the lead-time. If it takes, let's say, twelve weeks from when we receive demand to when we can supply, then we can try to shorten the lead-time by moving the supply line closer to the demand. When we measure the quantity base, this is the inventory. These two ways are looking at the same situation from different perspectives. These factors represent the effectiveness of the production system. Then, what is efficiency? We call added value as the efficiency. But, what exactly is added value?
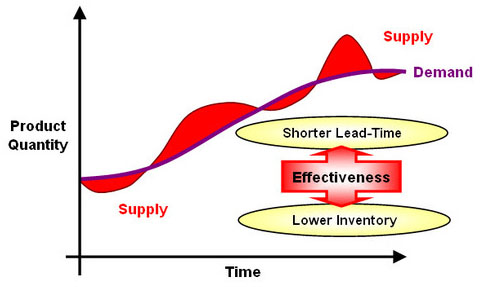
Fig 7. Greater effectiveness leads to shorter lead-times and lower inventory
Q. To produce something, you have a cost, so the added value is what you add to that cost to make a profit. It is what you are actually generating for profit?
A. That's right. So, the added value can be defined as the sales price minus the material cost. In our production system we know the sales price. We can calculate the costs which we pay out to external parties for raw materials or electricity etc. outside of our production system. This gives added value.
Q. In this case, would external costs also include the salary of the workers?
A. No, that's a very good point. The salary of the workers is paid from the added value. Added value is a kind of GDP, gross domestic product. GDP is a summation of all of the company's added value. There is another production system, which are the companies that we buy from the raw materials from. And there is probably another company that buys our product and sells them to the customer etc. So the sales and costs are totally cancelled out and the Gross domestic product is the total of all of the company's added value. There is also a term called productivity. This is defined in management science or in accounting. Productivity is a ratio of output to input. This is very general definition. For our case, added value is the output of the production system and the input is the manpower of the human working in the production system. Conventionally, we have used headcounts. But, recently, the employment system has changed. Many workers are part-timers or self-contracted workers so instead we often use man-hours instead of headcounts. Added value productivity is the measure of productivity of the production system. This represents the efficiency of the production system. The purpose of production management is to increase effectiveness and efficiency. The second aspect is the human factor. So let's suppose you won a kind of lottery and suddenly you became a rich person, wouldn't that be nice? In such a case, what would you do?
Q. If it were I then maybe I'd spend some, and then save some.
A. One of my friends asked me, "What would you do, Sato-san, if you suddenly won 500 million dollars? That far exceeds the lifetime income of a typical worker, so that means that we don't have to worry about having an income. In such a case, which job would you choose?" "Hey, do I have to choose a job?" He said, "Yes. Because if you are simply idle or lazy then you will go crazy". He said that currently he was working for his company, which is both a consequence of some kind of coincidence and his choice, right? And, yeah, it's exactly the same for me. But, sometimes he imagines, what job would be better if he can forget about the income and he said, "It would be nice to be a train driver". The point I want to make is if I won 500 million dollars would I continue current work? Would my work still interest me? This is a very basic question, right? So, if craftsmen are working in a factory, are they still willing to continue working as craftsmen, even if they became millionaires? Probably the purpose of production management is to create a workplace so attractive that every worker would still want to continue working there even if they won the lottery. This is the human factor and this kind of human factor is unfortunately either forgotten or ignored. We must never forget that added value is only created by humans so the most important thing is to make sure that these people are comfortably and happy. If we divide the work process in to a piecemeal type of thing, like Charlie Chaplin's Modern Times, as you know, a kind of belt conveyer where you work all day then this isn't very attractive. It may be effective, or even efficient but it doesn't make people happy when working. So, the production management has two quite contradicting purposes. To make the production system both efficient and effective, and at the same time, keep the people comfortable and happy. Sometimes, in a lucky case, we can match them exactly but most often there is a tradeoff between these objectives. And even for effectiveness and efficiency there is a tradeoff as well. That's why the plant manager is required and this is only thing he has to do.
Q. So the plant manager is trying to make his factory as productive as possible, while at the same time, making sure that it's a good place for his workers to enjoy their work.
A. I think the purpose of Lean Manufacturing is to somehow meet these objectives simultaneously.
Q. In the past, when workers were cheap, it was often the case that the workers were treated badly, even in the Toyota Production System. In the beginning the workers were treated like any other machine, and that's changed now. But, is it difficult to balance the system? How do people decide which is more important? Is there a category that the plant manager should follow when trying to balance these objectives?
A. Well, the plant manager is also just one part of the whole enterprise, and someone else is driving this plant manager. What kind of measurement is used for his evaluation? This is another key but it concerns a higher issue about management, so I want go in to detail about that now.
Q. You've given us a very good example of how production management fits into the production system. Now, the next stage is the product planning itself. How does that develop within this overall hierarchy?
A. Let me put it in this way. What is planning?
Q. For example, you want to go to Tokyo on holiday. You have a goal and you have various means to achieve that goal, and so planning is to decide which of those means you use to achieve your goal. Do you want to go via the quickest route, or the cheapest route, or the most interesting route? Deciding how you want to do it with all these different factors is what you could call planning.
A. Exactly and the planning activity can be broken down into three steps. Firstly, identify tasks. From the start to the overall goal we can break down the process into controllable pieces or meaningful steps or some alternatives. So the first thing in planning is to identify tasks. The second task is to assign the resources to these tasks. The production is done by many people in a collaborative way so we have to decide which person or which production line will be used for which task? Finally, the third step is to create the timetable and in another sense this is the scheduling. These three steps are planning. In some cases, the sequence is different. It depends on which task is the bottleneck, the resource or the time. For example, if time is limited and the resources are abundant then probably as the second step we should create the timetable first and then assign the resources. But normally we first assign resources and then create the timetable. Which way is workable? It depends on the situation.
Q. You've been to many companies and taken a look at their production system and the management. Normally, which area do you have the most trouble with? When you look at a company and say, "You can do better", which area do most companies need to focus on, is there a typical problem that most companies suffer from?
A. That's a good question. In Japan, the main issue that I've been seeing is kind of a paradigm shift from let's say the 1960's or 1970's, when this country was rapidly growing. At that time the production system was producing things without being driven by demand information. And in such a case, the plant or company itself was run on the production style of make-to-stock. Now, from the 1990's to 2000 we are living in the market situation so, we are forced to shift to make to order or assemble-to-order. However, the management perspective or the management control measurement for the production system was still in the previous age, so as much as you make, is the best way. I've seen many plants and companies and the biggest thing is they did not change their mindset from the good old 1960's and 70's. All the rules and measurements of production are still set in the good old days to maximize the product quantity. However, the sales division wants different things everyday, and they change what they want every day. This is the main contradiction inside manufacturing companies.
Q. So that's why that production planning now is more important than it was before, and it will become even more important?
A. Because markets are changing. If the markets change rapidly then it's more difficult to fit a supply line to the demand of the changing market.
Q. As you mentioned, using a production scheduler can help in one of the three tasks, the creation of the timetable. However, if you don't have the overall planning in place, and you only try to use the scheduler, what problems happen? Can you try to only concentrate on the timetable without thinking about the other tasks as well?
A. In order to use the scheduler in such a way, you have to have the entire inventory for the raw materials in high stocks piles. Then all you have to do is to assemble it, right? However, suppose that you don't have any raw materials or parts, or you try to minimize that kind of inventory, and the demand is changing every day. Then, what kind of schedule can you create? The scheduler can process things only if the raw material is available at the right timing. In such a case, that bottleneck is purchasing, not the production. That's why I say, planning is so important. The planning provides a base of rough supply curve that the scheduler can fit more precisely. Without planning, you cannot make that happen. The other strategy of course is to pile up all the raw materials and parts in the warehouse, but that's not efficient any more.
Q. On the other hand, if you have a production system with really good planning, do you really need a scheduler? A lot of companies think that they have their factory planned well, and that they don't need a scheduler as well, or they can do it by hand. Is it really important that they implement a production scheduler, or is it possible to do good planning without a scheduler?
A. It depends on the situation. For example, if you have only one product, you don't need scheduler. However, the more product families you have, the more you need scheduling. Also, the quicker your markets change, the more you need scheduling.
Q. Many companies started small a long time ago, and they have slowly gotten bigger. As they've gotten bigger, the market has changed as well. Some of these companies have slowly changed their mindset, and have been able to adapt, while other companies have been very slow, and then they suddenly try to change. For those companies now, who realize that the way they're managing the factory is not appropriate, how should this kind of company go about changing the way that it manages its production? I guess they contact a company such as yours to assist. Do you have any advice for companies who need to change? What things should they consider before they change?
A. That's a very difficult question. Mindset cannot be changed in one day or even in one year. It takes a very long time, so there is no simple answer.
Q. You mentioned on a previous occasion that when you go to a company, first of all you explain the concept, and if they don't understand the concept, then you explain the method. And then if they don't understand the method, you then show them the means. And finally, if they can't implement the means, you give them a scheduler and just say, "OK. Do it like that." If they have a tool, then, even if they don't understand it, at least they have some sort of data by which they can see whether they are meeting their goals or not. Would you still suggest that as a way for a company, who can't understand? Can they can use some sort of tool or some sort of idea to change the way they think?
A. Well, I should say tactics cannot fill out a lack of strategy. So, a scheduler cannot fill out the lack of planning. A scheduler can improve some things, but the improvement is smaller, compared to the situation when they change the way of production planning.
Q. Finally, do you have any additional comments or advice that you would like to add to what we've talked about here? Maybe some companies have listened to this interview, and they think, "Oh, yes, we need to change." Or, "We agree with your system." Most of them will say, "Well, what should we do? You know, we've listened, and we agree, and we'd like to change our company." What advice would you give them for their first step?
A. We should reconsider about the measurement. Do not believe the measurement is given from the heaven. Simply having the fastest production line may not be the best measurement factor or criteria. In many cases, those measurements were set in the good old product-out days and people are still trying to fit into that measurement or that kind of direction. The most important thing is to reconsider what is the best measurement for the production system, rather than sticking to the same old measurement. What is Lean Manufacturing? What is lean? Lean means to fit the supply curve as closely as possible to the demand curve. This is something where if you are fat, you may have too much stock, right? But, stock is not the only good measurement for production system. Lower cost, this is not the only governing measurement either. If we only pursue cost reduction, then we would probably cut the salaries of all those direct workers or subcontract the work. In such a case, the cost will be reduced, but you will have forgotten the human factor and your production system will slowly deteriorate. So, please reconsider the way you measure your production. That is the starting point.
Q. When they do consider how they should be measuring the goals of the factory, then they will come to understand how they should better manage it and better plan it so that they achieve these goals.
A. That's right. The production system is a very big, complicated system, so it's quite difficult to understand in one shot. Therefore, people tend to set piecemeal measurements and drive people in piecemeal. It makes things much more complicated and worse.
Q. In a big company, when everybody has different measurements, that's when things become difficult. Is it also important that when you do decide a measurement that you make sure that it's the same measurement for everyone in the company?
A. Yes, in a consistent way.
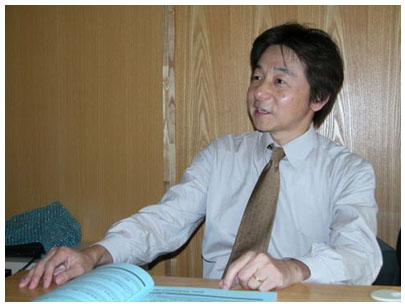
Fig 8. Tomoichi Sato is a veteran project analyst who has already published
numerous books on Production Scheduling and Project Management.
» More Information