|
Lean Tools and Techniques |
|
Agile Manufacturing: A manufacturing approach designed to contribute to the flexibility of a process resulting in the impact of changes in product mix and volume Autonomous Maintenance: A component of total productive maintenance that involves production machine operators in step-by-step activities to ensure optimum conditions of machine operation. Baka-Yoke: A Japanese term meaning ¡°fool-proofing.¡± Abandoned by Shigeo Shingo in favor of the term poka-yoke
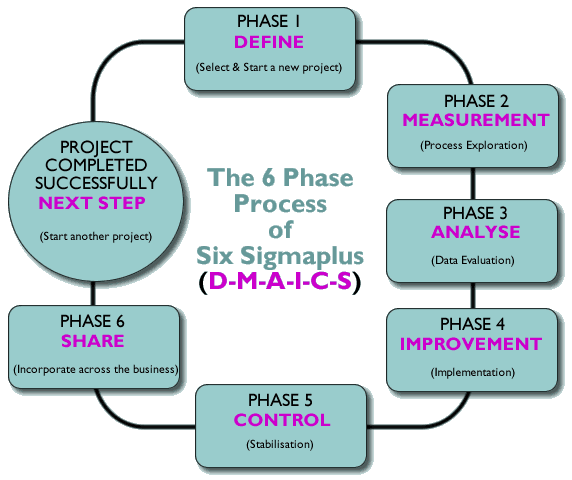
Balanced Scorecard: A measurement system that helps a company to translate its vision and strategy into action. It identifies metrics against the intent of the current plan and gives weight to the most important. Bar Code: A sequence of vertical bars and spaces that can be read by a light sensitive laser beam and translated into digital data used by a computer. It is used for tracking parts through manufacturing, warehousing, and shipping Build to Schedule (BTS): A measure of how well a plant produces the correct volume, mix, and sequence according to customer requirements. Cellular Manufacturing: Manufacturing by the use of cells Changeover Time: The time between the last good piece off one production run and the first good piece off the next run Current Reality Trees: Is a problem-analysis tool, aids to examine cause and effect logic behind our current situation Conflict Resolution Diagram: Also referred to as ¡®evaporating cloud¡¯ is used to resolve hidden conflicts that usually perpetuate chronic problems Dock-to-dock Time (DTD): A measure of the speed of product through the factory. It is the time between the unloading of raw materials and the release of the finished product for shipping Economic Order Quantity (EOQ): The batch-sizing calculation resulting from a break even analysis in which both allocated changeover costs and inventory carrying charges are at their lowest. Error Proofing: Error Proofing is a structured approach to ensure quality and error free manufacturing environment. Error proofing assures that defects will never be passed to next operation Failure Mode and Effects Analysis (FMEA): The analysis of a product to ensure that its potential and future failures are identified and fixed Fault-tree Analysis (FTA): A review that takes a backwards look at failures, faults, defects, and shortcomings First-time-through (FTT): The percentage of good units completing any sub-processes determined by dividing the number of units minus any defects by the total number of units Five Ms: Five words beginning with the letter M that describe the five areas of production where quality problems can occur. They are man, machine, materials, methods, and mother nature. Five S: A methodology for organizing, cleaning, developing, and sustaining a productive work environment. Improved safety, ownership of workspace, improved productivity and improved maintenance are some of the benefits of 5S program Five Whys: The practice of asking ¡°why¡± five times to help identify root cause of a problem. Focused Equipment: An approach that focuses on specific equipment parameters or capabilities to improve Improvement (FEI): overall equipment effectiveness. It is applied in the later stages of total productive maintenance. Future Reality Diagram: Is a sufficiency based logic structure designed to reveal how changes to the status quo would affect reality ¨C specifically to produce desired effects. Heijunka Box: A physical device used to level production volume and variety over a specified period. It visually displays product family and is divided into slots that are loaded with kanbans that represent customer orders. Hidden Factory: Activities, people, and processes that produce waste and inefficiency. They do not add value and are often overlooked. Inventory Turnover Rate: The number of times an inventory cycles or turns over during the year. A frequently used method to compute inventory turnover is to divide average inventory level into annual cost of sales. JIT: A philosophy of manufacturing based on planned elimination of all waste and continuous improvement of productivity. It encompasses the successful execution of all manufacturing activities required to produce a final product Kaizen: The Japanese term for improvement; continuing improvement involving everyone ¨C managers and workers. In manufacturing kaizen relates to finding and eliminating waste in machinery, labor or production methods. It is composed of the Japanese ¡°kai¡± meaning ¡°to take apart¡± and ¡°zen¡± meaning ¡°to make good.¡± Kanban: Kanban is a simple parts-movement system that depends on cards and boxes/containers to take parts from one workstation to another on a production line. The essence of the Kanban concept is that a supplier or the warehouse should only deliver components to the production line as and when they are needed, so that there is no storage in the production area. Lean Metric: Lean metrics allow companies to measure, evaluate and respond to their performance in a balanced way, without sacrificing the quality to meet quantity objectives, or increasing inventory levels to achieve machine efficiencies. The type of the lean metric depends on the organization and can be of following categories; Financial performance,behavioral performance and core process performance Likert Scale: A measurement method used in attitude surveys. Responses are typically on a five to seven point scale that ranges from ¡°strongly agree¡± to ¡°strongly disagree.¡± Management by Walking Around (MBWA): A management style where leaders make themselves accessible and helpful by walking around the shop floor and office to see what is going on. Material Requirements Planning (MRP): A computer based system used to determine the quantity and timing of the supply of production materials. It includes a master production schedule, a BOM, and current inventory information. Mean Time to Repair (MTTR): A rating that indicates the average time in which maintenance operations can be performed to either prevent or correct malfunctions. It is equal to the total downtime for repairs divided by the number of repair incidents. Mistake-Proofing: An improvement technology used to prevent defects or equipment malfunction during order taking or manufacture. Also referred to as ¡°poka-yoke.¡± One-piece Flow: One-piece flow or continuous flow processing is a concept means that items are processed and moved directly from one processing step to the next, one piece at a time. One-piece flow helps to maximum utilization of resources, shorten lead times, identify problems and communication between operations One-Touch Exchange of Die (OTED): Minimizing machine changeovers to the point where they can be performed in less than one minute or with a single touch. Overall Equipment Effectiveness (OEE): Measures the availability, performance efficiency, and quality rate of equipment ¨C it is especially important to calculate OEE for the constrained operations Overall Supplier Effectiveness (OSE): The cost of doing business with suppliers. OSE = percent of defects x cost variances x percent of missed deliveries. Poka-Yoke: Japanese term for mistake proofing. Predictive Maintenance: A maintenance component of total productive maintenance based on machine history and data based equipment knowledge. Predictive maintenance methods are used to pro-actively predict potential problems. Prerequisite Tree: Is a logical structure designed to identify all obstacles and the responses needed to overcome them in realizing an objective. It identifies minimum necessary conditions without which the objective cannot be met Preventive Maintenance: A maintenance component of total productive maintenance that is based on the critical operating characteristics of the equipment and their operating ranges. It is scheduled at predetermined intervals to achieve continuous operation of equipment. Process Mapping: A method used to understand the flow of activities within a process. It enables those unfamiliar with a process to understand the interplay/interaction of activities during the workflow. Process Route Table: Shows what machines and equipment are needed for processing a component or assembly. These tables aid in creating ordinary lines and grouping work pieces into work cells Pull Production: A system of production and delivery in which nothing is produced by the upstream supplier until the downstream customer signals a need. Push Production: Conventional production where production schedules are pushed along based on sales projections and availability of materials. Quick Changeover: Quick changeover is a technique to analyze and reduce resources needed for equipment setup, including exchange of tools and dies. Single Minute Exchange of Dies (SMED) is an approach to reduce output and quality losses due to changeovers Repeatability: A variability value determined by a number of measurements with the same instrument by the same appraiser on the same characteristic. Reproducibility: A variability value determined by a number of measurements with the same instrument by different appraisers on the same characteristic. Robust Design: A design that is not sensitive to variations from its inputs or to deviations from its underlying assumptions. Scatter Diagram: A diagram that uses data points to plot a pattern that shows the relationship or correlation between pairs of variables or factors. Set in Order: The second activity in 5S involving identifying the best location for each item kept in an area. Seven Muda: Ohno¡¯s original categories of non-value-adding wastes found in production. They are overproduction, waiting, unnecessary transport of material, overprocessing of parts, excess inventory, unnecessary movement, and production of defective parts. Sigma: The Greek letter used to describe the standard deviation of data. Sigma measures how much a process varies from perfection. Silos: Vertically organized functional departments. Lean organizations use cross-functional teams to break through the walls of silos. Single-Minute Exchange of Die (SMED): A series of techniques that result in production machinery changeovers in less than ten minutes. Single-Piece Flow: See one piece flow Sporadic Loss: The difference between actual equipment effectiveness and its optimal potential when a loss increases suddenly beyond its usual range. Standard Rate of Work: The length of time that should be required to set up a given machine or operation and run one part, assembly, batch, or end product through that operation. This time is used in determining machine requirements and labor requirements. Strategic Planning: Planning done at top management level to establish broad directions and initiatives of a company. Successive Changeover: A changeover method in which each machine is changed over as soon as its current step is no longer needed. Supermarket: Storage of a set amount of finished goods or WIP within the value stream to allow for a pull system when continuous flow is not possible. Supply Chain: All suppliers involved in the manufacture of any component used in a particular end product. It begins with the manufacturer of the component and ends with the manufacturer of the end product. Taguchi Methods: A form of experimental design developed by Genichi Taguchi used to achieve near optimal quality characteristics (reduce variability) for processes and products. Takt Time: The time required between completion of successive units of end product. Tact time is used to pace lines in the production environments in order to satisfy market demand. It is determined by dividing the available production time by the rate of customer demand. Theory of Constraints: A management philosophy developed by Eliyahu Goldratt that every company has constraints or it would be making infinite profit. The five-step process of eliminating or reducing constraints are: 1) identify the constraint; 2) decide how to exploit the constraint; 3) subordinate all other resources to solving the restraint; 4) elevate the constraint; 5) if the constraint has been solved, return to step 1. Total Productive Maintenance (TPM): Total Productive Maintenance (TPM) is a maintenance program concept, which brings maintenance into focus in order to minimize downtimes and maximize equipment usage. It enlists operators in the design, selection, correction, and maintenance of equipment to ensure that every machine or process is always able to perform without interruption or slowing down defect-free production. Included in TPM are autonomous maintenance, early equipment management, focused equipment improvement, predictive maintenance, and preventive maintenance. Total Productivity Management (TP Management): A management approach used to organize and prioritize activities of customer-oriented product manufacturing. It involves coordinating objectives coming from the top down with proposals and strategies rising from the bottom up. Total Quality Management (TQM): An approach with the premise that all operations have a quality aspect that can be perfected. It requires effort from every person in the company. TQM is also called total quality control (TQC). Toyota Production System: The Toyota production system is a technology of comprehensive production management. It is built upon three key factors: reduced lot size (to allow for production flexibility), the control of production parts (so that parts are always available when and where needed), and the arrangement of production equipment in logical order of assembly. The basic idea of this system is to maintain a continuous flow of products in factories in order to flexibly adapt to demand changes. Transition Tree: Is a cause and effect logic tree designed to provide step-by-step progress from initiation to completion of a course of action or change. It is an implementation tool Type 1 Error: Rejecting the null hypotheses when it is true. A relationship between two variables is assumed to exist when none actually does exist. Type 2 Error: Accepting the null hypothesis when it is false. A relationship between two variables is assumed not to exist when one actually does exist. Value added to Nonvalue added Lead Time Ratio: Provides insight on how many value added activities are performed compared to non value added activities, using time as a unit of measure Value Stream Mapping: Value stream mapping is a graphical tool that helps you to see and understand the flow of the material and information as a product makes its way through the value stream. It ties together lean concepts and techniques Visual Factory: The application of visual control and a visual management system on the shop floor. Visual Management: Is a set of techniques that makes operation standards visible so that workers can follow them more easily. These techniques expose waste so that it can be prevented and eliminated Visual Metrics: Displaying measurements important to maintaining and improving operations and processes. Workflow Diagram: Shows the movement of material, identifying areas of waste. Aids teams to plan future improvements, such as one piece flow and work cells. Zero Changeover: A changeover that is performed in less than three minutes or within one production cycle. Zero Defects: The concept (introduced by Philip Crosby) of manufacturing products that have no defects. Zero Quality Control (ZQC): A quality management system that includes self inspection by operators, successive inspection of incoming quality by operators, and the use of mistake-proofing devices to control quality at the source.
» More Information |
|
|
|
|
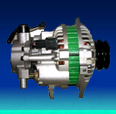 |
RB-ALT092 |
|
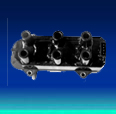 |
RB-IC8046 |
|
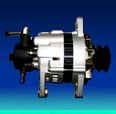 |
RB-ALT090 |
|
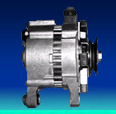 |
RB-ALT040 |
|