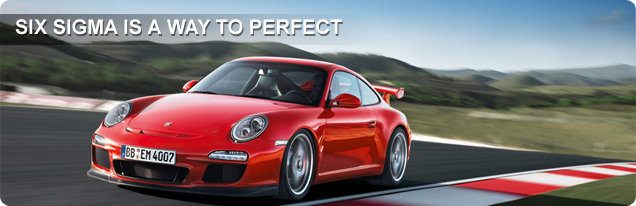
Many of these terms are very specifically related to Six Sigma. Others are used in a general 'quality management' context and also in Six Sigma. As already explained, Six Sigma tends to embrace many other methodologies. A few of these terms are quite technical since they occur in the statistical, engineering and mathematical aspects of Six Sigma.
acceptance, and acceptable quality level (ACL) - Acceptance has at least two different meanings in Six Sigma terminology, so be careful to understand which one is being referred to. Firstly, acceptance relating to quality is the quality expectation of the customer, internal or external. Acceptable Quality Level (ACL) means the same basically, in more formal Six Sigma-speak, and which will frequently be expressed in terms of percentage defects. Secondly acceptance refers to the buy-in or agreement of people affected by proposed actions and changes, notably stakeholders. While not strictly part of the Six Sigma battery of supporting tools, I can strongly recommend Sharon Drew Morgen's facilitative communications concepts for anyone struggling with stakeholder acceptance (and wholesale organizational change as well for that matter.)
activity report - A simple tool which enables teams and team leaders to manage project management tasks, responsibilities and timescales.
affinity diagram - A diagrammatic method of capturing, analyzing and organizing lots of ideas, elements, activities, etc., that together represent or influence an overall category, such as a process or issue. The brainstorming method is central to structuring an affinity diagram, and 'post-it' or sticky notes are commonly used as a way of generating and organizing data. Commonly used in brainstorming solutions during the Improve stage of DMAIC.
analysis - Analysis of all sorts of data is a critical component within the Six Sigma model, which involves using various analytical methods to identify and quantify the causes of quality variation and failure in specific processes. Various analysis perspectives are adopted, for example:
• discrete - looking at a particular failure or problem ¨C e.g., using Pareto ('80:20') or pie-charts to show causes by percentage
• continuous - mapping performance variation and types, etc., over time, using distribution graphs
• process - creating detailed flow-diagrams to understand what's really going on in the process or sub-process
ANOVA, ANCOVA, MANOVA, MANCOVA - Despite first impressions these are nothing to do with Russion gymnastics or ice-skating moves. ANOVA is an acronym for analysis of variance, a specialized variation calculation method concerned with comparing means and testing hypotheses, best left to engineers and mathematicians. So are the related methods, ANCOVA (analysis of covariance), MANOVA (multiple analysis of variance), and MANCOVA (multiple analysis of covariance). Unless you are an engineer or a mathematician you will almost certainly have better things to do than get to grips with this level of statistical capability. Terms such as these illustrate why we need to work in multi-disciplined teams.
balanced scorecard - A sophisticated strategic analysis and improvement methodology developed by Kaplan and Norton which in its own right can sit outside Six Sigma, but which can be included within Six Sigma methods, and in any event might be used or referenced in the context of quality and performance improvement. The 'balanced scorecard' identifies, correlates, 'balances', measures and drives improvement across a wide variety of factors that are deemed responsible for overall organizational effectiveness, and for meeting customer expectations. The tool essentially translates strategy into operational metrics, and according to Motorola (i.e. in a Six Sigma context) typically features the perspectives of, vision, current initiatives, business processes, and business results. 'Balanced Scorecard' became a generic 'brand' for business improvement in the 1990's, rather like Six Sigma, although arguably not on such a grand scale.
black belt - A specific Six Sigma term to describe a team leader and one who has achieved accredited 'Black Belt' qualification via an appropriate training course.
black noise/white noise - Technical terms relating to respectively non-random and random causes of variation.
business improvement campaign - A Motorola Six Sigma buzz-phrase, which represents a leadership initiative to improve the business's 'big Y's'.
business process management - A common generic expression in its own right, but also a Six Sigma term for the initial strategic element of Six Sigma. Six Sigma's strategic first phase is designed to develop management's commitment to Six Sigma, and also management's active participation in the Six Sigma process (which suggests why a powerful brand name for the initiative, ie., Six Sigma, is helpful..). This amounts to identifying the key processes within the organization that determine effectively meeting customer expectations; then measuring the effectiveness and efficiency of the processes (notably measuring variation in quality and analyzing the causes), and then initiating improvements in the weakest processes, which should logically yield the greatest results and return on effort.
cause-effect diagram - Also known as the fishbone diagram, this is a generally used tool for mapping and analyzing causal factors towards an end output, so that contributing factors (and weaknesses can be more easily identified). Used especially in Six Sigma as a team brainstorming analysis tool. Called a fishbone diagram because the diagram plots contributing factors along parallel diagonal lines which each join a central horizontal time-line (like the back-bone) which culminates at one end with the main issue or question.
CTQ - Critical To Quality - An element within a process that has a major influence on the process quality, and typically the quality of a critical process, or it would be unlikely to be receiving Six Sigma attention.
defect - A vital and generic Six Sigma term for any failure in meeting customer expectation (internal and external customers) - any failure within the delivery process.
DFSS - Commonly used abbreviation in Six Sigma activities and communications, it means Design For Six Sigma, and describes the method of using tools, training, measurements, and verification so that products and processes are designed at the outset to meet Six Sigma requirements. A more specific version is DMADV: Define, Measure, Analyze, Design, and Verify. Both DFSS and DMAVD are concerned with, and emphasize the importance of, using Six Sigma principles in product/process design, not just for remedial improvements - rather advocating that prevention is better than cure. Thus, if Six Sigma capability is built into new organizational systems and products when they are designed, so performance will be better, and the need for Six Sigma remedial effort will be reduced.
DMAIC/DMAICT - Central Six Sigma process and acronym to ensure you remember it: Define, Measure, Analyze Improve, Control, more recently extended to DMAICT by others in the Six Sigma consulting and training communities, to Transfer (transfer best practice and thereby share learning).
DMADV - An alternative/substitute abbreviation to DFSS (Design For Six Sigma), and like DFSS DMADV is central to Six Sigma initiatives. DMADV more specifically describes a method comprising linked steps; Define, Measure, Analyze, Design, Verify, for ensuring that products and processes are designed at the outset to meet Six Sigma requirements.
frequency distribution/frequency distribution analysis or checksheet - Frequency distribution and the checksheets and other frequency distribution measurement tools form an essential aspect of Six Sigma data analysis. Identifying frequency of variation in processes is central to Six Sigma, since customers are particularly sensitive to variation, arguably even more than isolated failures. Therefore the sampling and collection of data over many operations and extended time periods, and the use of this data to indicate the frequency (number of times) that a variation occurs rather than the size of isolated failures, is an essential perspective for truly understanding what's happening, and the causes, within any critical delivery process. Frequency distribution analysis is an excellent antidote for any temptation to respond to an isolated failure with a knee-jerk quick fix, such as shooting the messenger or bollocking the workers when something deeper in the process is awry.
green belt - A Six Sigma team member who has received Green Belt training and who works part-time on Six Sigma projects under the guidance of a Black belt team leader.
just in time (JIT) - Just In Time, commonly abbreviated to JIT, describes operational or production methods based on minimizing stock levels, the aim of which is to reduce capital employed in stock, which also has knock-on benefits to reducing storage space, decreasing dependence on logistics, easier supply chain management, and better overall quality. Just In Time is actually a capability arising from improvements within a business operation, rather than a cause of improvement itself. Introducing Just In Time methods without improving efficiency and reliability necessary to support it is not viable. Since Just In Time methods entail reducing stock levels to absolute minimum or even zero, JIT allows no room for error. Timing and predictability are crucial. JIT requires total commitment to quality and efficiency or the supply chain and related operations break down, the costs and implications of which can easily exceed any savings from JIT stock reductions. The term and methodology were developed by the Japanese during their post-war industrial revival (second half of the 1900s) as a logical progression from 'materials requirements planning' (MRP). The Japanese original terminology is 'kanban', and is important within 'lean production' methodology. The aim of kanban is actually zero inventory. JIT features in highly efficient manufacturing corporations, and has more recently been significantly enabled by computerization, especially to analyze and manage timings rather than stock levels. Noted authors to have covered the subject include Edwards Deming, Taiichi Ohno, and Yasuhiro Monden. The acronyms page contains a more amusing definition of JIT.
master black belt - A highly qualified Six Sigma practitioner, typically concerned with overseeing Six Sigma activities from an organizational perspective.
materials requirements planning (MRP) - production quality management methodology focusing on planning stock (materials and components of all sorts) levels and availability according to production schedules.
pareto principle, pareto diagram, pareto analysis - The Pareto Principle is otherwise and more commonly known as the 80:20 rule. The Pareto Principle was named after its originator Vilfredo Pareto, (1848-1923) an Italian economist and professor of political economics at Lausanne University, who first discovered the 80:20 'rule' of 'predictable imbalance', that (as far as Six Sigma is concerned) provides a basis for focusing on the 20% of activities that generate 80% of results, or the 20% of failures that are responsible for 80% of the waste, etc. Pareto first made his discovery while analyzing wealth distribution among the British, in 1897. The Pareto Principle is also known as The Parato Law, The Principle Of Least Effort, and The Principle Of Imbalance, which in themselves provide an example of the Pareto Principle in action because despite all the options, hardly anyone ever uses any other name than 'The 80:20 Rule'. More Pareto explanation and examples in use.
process - The word process is worth mentioning because it is a fundamental cause of confusion (and not just in Six Sigma, but that's another story). The word process is used heavily in describing how Six Sigma works, and it's also used heavily in referring to the service or production activities (processes) on which the Six Sigma methods (or processes) are directed. You see what I mean... It is both the subject and the object. People easily get confused by terminology at the best of times, so it's worth taking extra care when using words like process which have at least two distinctly different meanings. For example avoid phrases such as "Six Sigma is a process that uses processes to improve processes." It's true, but its a load of bollocks. So, when using the word process, check that people know what process you are actually referring to, and then you will have a fighting chance of not disappearing up your own backside.
process mapping - diagrammatical representation of how processes work, as could be used and developed in team meetings on a flip-chart, or other media, to enable teams to understand processes, participants, and where and how improvements might be made.
production planning - generic term describing the over-arching methodology used in managing the supply process from receipt (or forecast) of customer requirements through to delivery notes and invoicing. Production planning therefore includes:
• interpretation of customer orders/requirements
• works orders
• schedules and computer programs/ implications
• parts, stocks and materials
• machinery, plant, equipment availability and allocation
• people and teams
• quality and other targets - setting and monitoring
• stock and purchasing monitoring and records
• order processing, administration and accounting
• necessary inter-departmental liaison (e.g., sales, export, etc)
Production planning is typically highly modularized and computerized since process reliability is crucial and is systematically repeated, although production planning must also allow for variation in response to sales or other changing demands and product specifications. Production planning is generally a weekly and monthly requirement, as well as incorporating longer-term commitments and considerations. The particular sales environment and predictability of the market and business have major impacts on production planning. Volatile markets and unpredictable sales obviously make production planning more difficult. Costs and budgets, health and safety, environmental, and other indirect considerations or compliances are of course relevant to production, but not directly, and so are not included as integral parts of the process.
Q x A = E - a natty little formula advanced by Six Sigma writer George Eckes for emphasizing and assessing the need for Six Sigma projects to feature both strong technical quality (Q), and strong acceptance by the stakeholders of the project team's proposed solutions (A). E represents the excellence of the results, although why it should be E and not R rather defeats me. Whatever, the idea is a sound one, in that A is a multiplier and should along with Q should be assessed in simple terms at the early phase of a Six Sigma project. Eckes suggests scoring each of Q and A out of 10, and that if E equals anything less than 60 then the project is unlikely to succeed, with the implication to return to improving technical quality and stakeholder buy-in.
six sigma - how long have you got?.... at its most basic Six Sigma equates to 3.4 defects per million opportunities; at its most sophisticated (dare one suggest most hyped?..) Six Sigma is an organizational philosophy.
soft skills - skills required for managing people, relationships, acceptance and effective communications. A potential area of vulnerability in many Six Sigma implementations, because of the predominance of Six Sigma team leaders with strong process skills and attention to detail, which can sometimes be at odds with the abilities of intuition, empathy, rapport-building, relationship-building, and other 'soft' people-skills.
stakeholder - vitally important aspect, this one: stakeholders are not just customers, stakeholders are all the people who are affected by the solutions identified within a Six Sigma project, and all the people with some involvement in implementing the solutions.
tollgates - breaks for review between Six Sigma processes within any of the DMAIC stages.
tree diagram - pictorial representation of how a broad aim is broken down into detailed actions, and which belong to named individuals or departments. A mapping technique that promotes creative thinking towards detailed causes and effects and accountabilities. Helps to avoid tendencies for activities and accountabilities to be left too vague.
X's/big X's - Motorola Six Sigma-speak for factors or variables that have the greatest impact on the 'big Y's'.
Y's/big Y's - Motorola Six Sigma-speak for the most important business results and measures that are linked to critical customer requirements and expectations.
» More Information